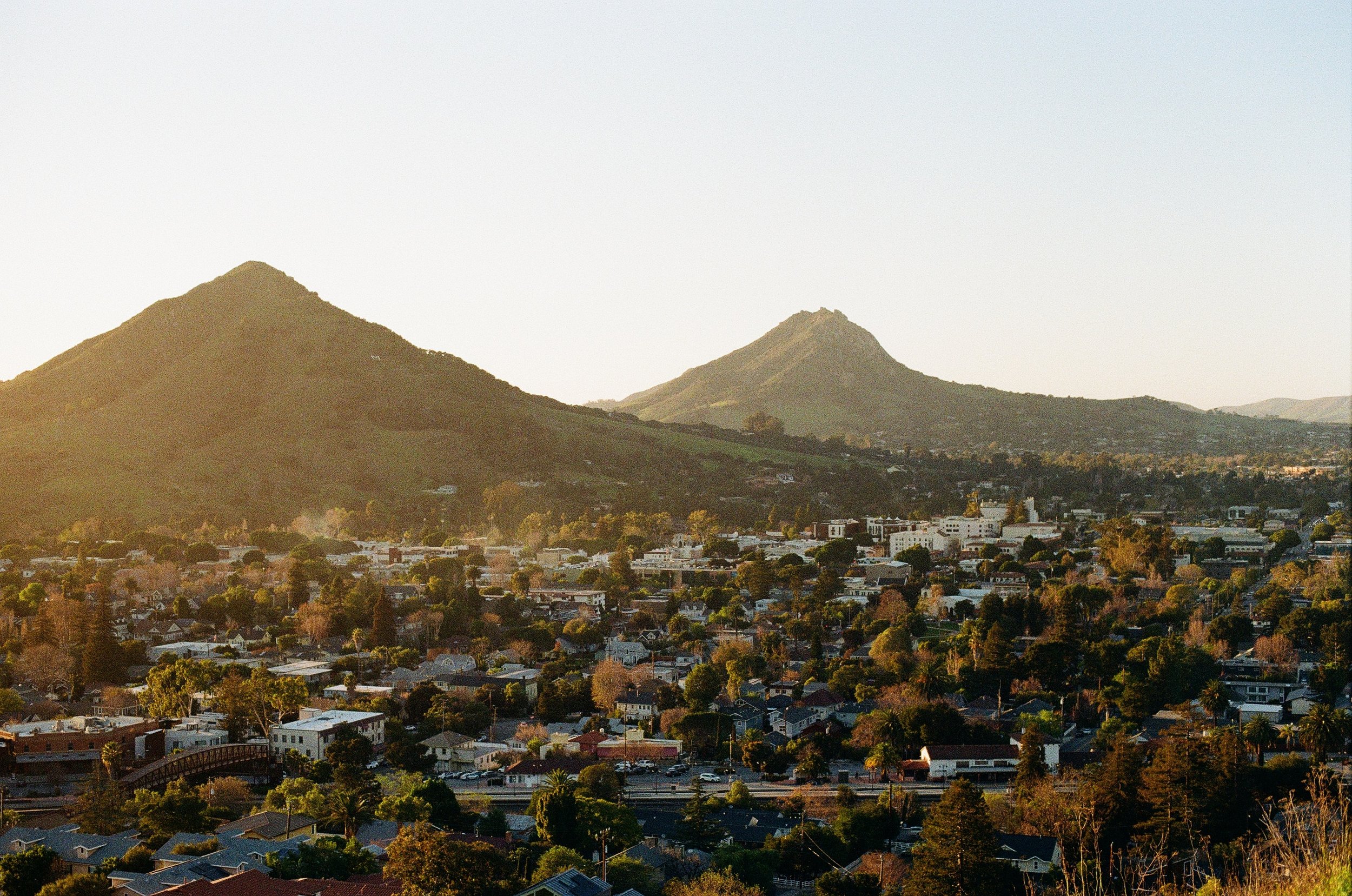
Bishop Passive House
Project Stats
Year: 2021
Type: Single Family Residence
Square Footage: 2,958
Achievements: Zero-Net-Energy, All Electric Home, Meets PHPP Criteria for Passive House
Bishop Passive is a one-story single-family residence near Bishop's Peak in San Luis Obispo, California. The project is all-electric, Passive House Certified, and uses approximately 85% less energy than the average newly-constructed home in California.
This home certification from PHI (The Passive House Institute) focuses on creating an efficient home to reduce the building's carbon footprint while increasing the user's overall comfort, health, and interior air quality.
The project incorporates a few key components necessary to achieve these goals. The home has continuous insulation throughout the living area and is an airtight construction assembly to ensure a more resilient shelter that maintains consistent interior temperature and comfort. The home subsequently requires only a tiny amount of space conditioning. Additionally, the project uses a balanced fresh-air-exchange ventilation system to ensure comfortable, clean indoor air quality.
During the design process, conscious decisions were made to choose building materials and finishes that would reduce harmful off-gassing and are recycled and repurposed when possible. This home is an example of how to build a resilient, efficient, comfortable, healthy, and cost-effective home.
Phase 1 - Design
Architectural Design by Cairn Collaborative
Environmental Consulting by In Balance Green Consulting
Phase 2 - Foundation
The slab for this project utilizes a new-to-us material called glavel.
Glavel is an insulating recycled glass aggregate that doubled as our gravel layer and our under slab insulation. It was surprisingly easy to install and gave us a smooth surface that got topped with our Stego membrane and our slab mixture. The foundation is both literally and figuratively the "foundation" of this whole project and it's a crucial step to pay attention to.
Phase 3 - Framing
Framing for this project was pretty much the same as on any conventional build. We did build a mock-up of the whole wall assembly on site that we used to show the framers how the entire wall was going to come together. This helped to keep the whole team on the same page on how the building was going to stay airtight.
Phase 4 - Water Control
We chose to use the Solitex Adhero Self adhering membrane for our weather resistant barrier. This membrane is diffusion permeable and helps to protect the exterior from weather while the construction is happening. In our wet winter this was definitely helpful. Two of us wrapped the entire house in a couple of days and we worked with the framers to tie this membrane into our roof membrane for a continuous wrap.
Phase 5 - EXT Insulation
For our exterior insulation we used Gutex Multitherm. It was incredibly easy for us to put up with our small crew, and would have been even faster if we'd taught the framing crew to do it. It was a breath of fresh air to not have to use foam and only go home covered in some sawdust. We used a circular saw to cut apart pieces and a staple gun to attach to our sheathing.
Phase 6 - Windows
Triple Pane windows were a must for this project. The client had some amazing views which meant we wanted to celebrate those with glass without compromising our airtightness. We went with ZOLA windows after checking out a couple of the high performance companies. They were able to make our large custom windows and doors. We ended up using a suction cup machine and a lot of arm strength to get these windows set into place. Once in the rough opening, it was incredibly easy to plumb them up. The thermal difference and sound difference was incredible upon the addition of this glass.
Phase 7 - Siding/Stucco
Phase 8 - Mechanical
For our mechanical system, we used a mini split to condition the home and an HRV to supply ventilation to the home. We went with a heat pump hot water heater to create an efficient system. The whole house uses no gas and therefore uses a heat pump dryer and an induction cook top. The energy usage for this home will be much less than a conventional build. We make sure to document all the water and ventilation lines before the drywall is put up. Key dimensions will help if there is any need to get into the walls in the future. This is given to the homeowner once the build is complete.
Phase 9 - Drywall

Want a deeper look?
Check out our Building Passive Video Series.
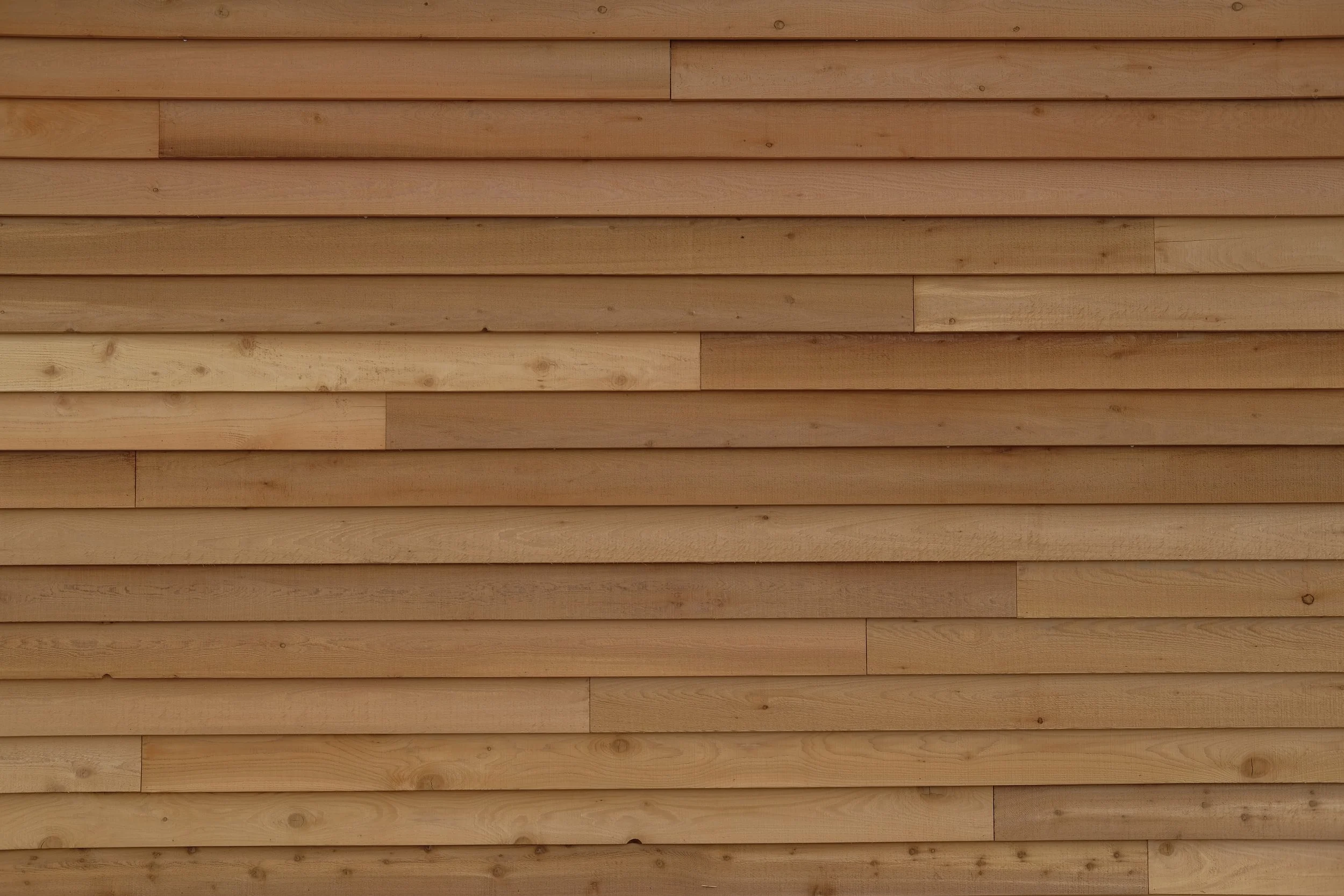